康士伯数字一体化生产管理系统,助力中海油数智化转型升级
深海一号气田是中国首个自营深水大气田,已探明地质储量超过千亿方,目前已正式投产,高峰年产气量超过30亿立方米,可满足粤港澳大湾区四分之一的民生用气需求,是供给粤港澳大湾区和海南自贸港的清洁能源的主力气田之一。深海一号的水下生产系统(约1500米),海床温度低(约2.6℃),采用了全水下井口的开发模式,具有水下生产系统复杂度高,操作动态频繁的特点。由于海管温度低,地层井流携带凝析液和水,会导致海管系统中流型复杂,存在诸多生产流动性保障难题与挑战,例如段塞,水合物,腐蚀以及停输再启动等。同时水下生产系统的操作变化,以及多相混输导致的井流不稳定性,都需要由平台上主体工艺来承担,因此水下系统和平台工艺一体化模拟和综合动态分析,成为安全生产和优化管理的必要手段。
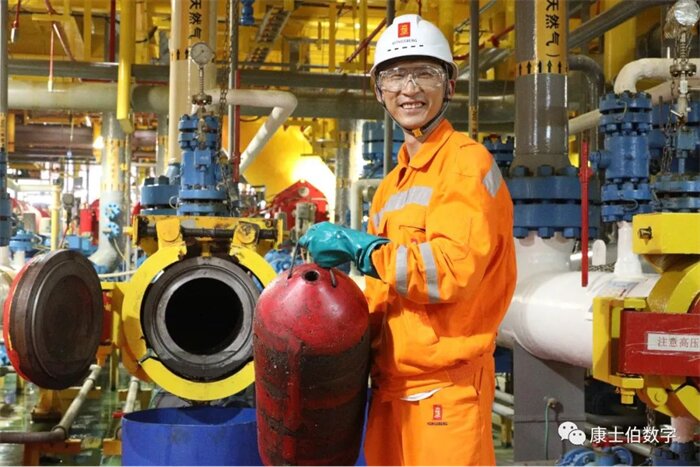
深海一号使用了康士伯数字所提供的一体化生产管理系统,实现了一体化模型分析,科学指导生产提产稳产,防范并预警油田生产运行过程中面临的安全风险。系统建立了一套包含气井、管道、平台主工艺全流程的仿真系统,用于生产辅助决策,在深海一号气田投产准备过程中进行了虚拟调试与试生产研究,针对不同的生产工程给出对应的流动保障建议,为投产方案的制定提供了理论指导及计算依据,保障了气田安全顺利投产。该系统还可用于开展海管段塞积液分析、水合物风险评估、抑制剂循环优化、清管作业方案评价、配产提产方案验证、生产工艺瓶颈诊断、平台工艺参数优化、能耗分析与管理等方面的研究工作。
该系统使用了基于机理模型的计算内核,开发在线监测、预测预警、虚拟仪表等功能应用及时发现问题和故障,并获得防范措施和操作建议,并接入实时生产数据。通过机理模型的在线模拟计算,实现了全流程工艺链的透明化管理,达到了全线全方位远程监控能力,使生产管理控制过程的工作模式发生了彻底转变,由以前的事后处理转变为事前预控和事中监测,整个生产过程的管控质量和决策质量取得了有效提升,极大地提高了生产时率和生产产量。
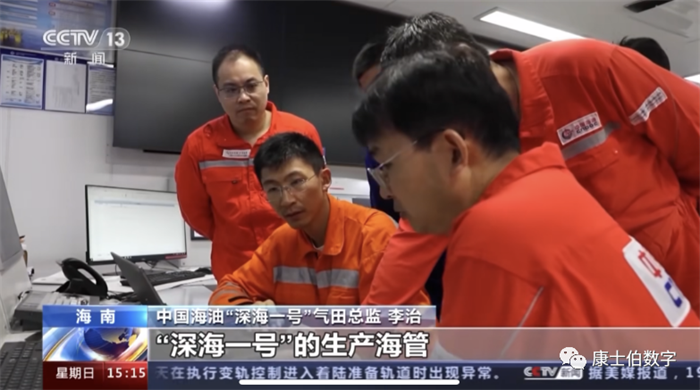
该系统还可用于解决不可测工艺参数的在线计算,工况动态预测,工况分析和设备状态监测。
将传统仪器仪表无法直接测量的生产数据,通过在线模拟计算的虚拟仪表,直观定量地展示给操作人员。例如管道的实时积液动态,药剂的浓度分布,水合物抑制剂效果,工艺流体的动态组分平衡等。将以往的监测盲区透明化,工艺分析颗粒度也更加的细化。
将设备状态监测与工艺动态相结合,与设备厂家针对撬装本身的分析工具实现了良好的互补结合。以往设备分析主要关注于分析设备本体的相关数据,与工艺数据的结合不深。通过系统中的设备状态分析算法,将外输压缩机和油嘴的工艺表现,与设备的工作状态结合,从工艺的角度反向评估设备运行的健康度。实现了伴随工艺生产的持续分析,对于工艺专业和设备维修专业的综合针对,给出了创新的解决方案。
将仪表偏差问题和潜在的风险信息,通过模型进行分析。这是以往仅通过人为的观察分析难以实现的。模型在持续计算和比对测量数据过程中,也在对每个仪表进行统计分析。同时,模型的计算结果也给了生产人员对于工艺变量的理论参考,帮助识别和分析出仪表数据后的生产价值。
工艺生产场景的定量分析,将以往在生产中通过经验探索或定性分析的场景,在动态模型上实现定量化、场景化的分析。例如,对丙烷丁烷在工艺系统中滞留问题的分析,通过模型实现实时动态的物料平衡分析。例如,解决压缩机流量计核验和产量匹配问题,通过压缩机模型实现虚拟流量计和流量匹配。例如,清管操作中的清管球位置跟踪,通过多相流清管模型,实现对清管球位置的在线显示。再例如,脱水脱烃工艺与上下游工艺操作设点之间的相关性分析,通过模型的离线模式,实现根据当前真实生产工况的流程模拟分析。随着气田的生产,类似的生产挑战和分析需求,均可考虑通过模型实现更加精确、定量的分析。
一体化生产管理系统的良好应用,体现了生产操作工具向着数字化、智能化方向的升级,体现了油气从业人员技术素养和专业能力的提升,是深水油气在数字化智能化转型中的成功落地。
更多详情,请关注“康士伯数字”微信公众号
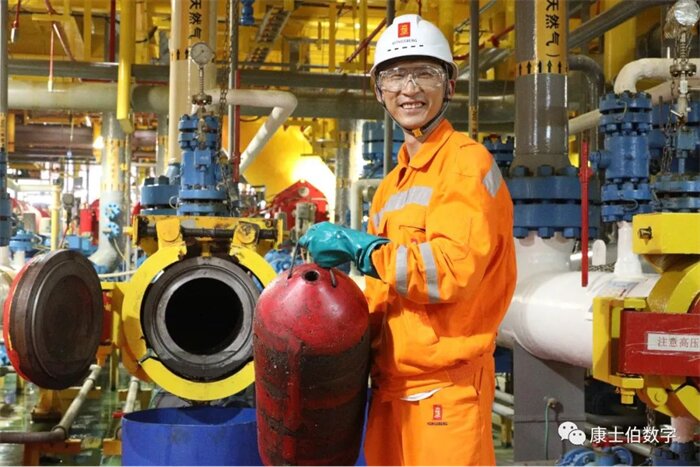
深海一号使用了康士伯数字所提供的一体化生产管理系统,实现了一体化模型分析,科学指导生产提产稳产,防范并预警油田生产运行过程中面临的安全风险。系统建立了一套包含气井、管道、平台主工艺全流程的仿真系统,用于生产辅助决策,在深海一号气田投产准备过程中进行了虚拟调试与试生产研究,针对不同的生产工程给出对应的流动保障建议,为投产方案的制定提供了理论指导及计算依据,保障了气田安全顺利投产。该系统还可用于开展海管段塞积液分析、水合物风险评估、抑制剂循环优化、清管作业方案评价、配产提产方案验证、生产工艺瓶颈诊断、平台工艺参数优化、能耗分析与管理等方面的研究工作。
该系统使用了基于机理模型的计算内核,开发在线监测、预测预警、虚拟仪表等功能应用及时发现问题和故障,并获得防范措施和操作建议,并接入实时生产数据。通过机理模型的在线模拟计算,实现了全流程工艺链的透明化管理,达到了全线全方位远程监控能力,使生产管理控制过程的工作模式发生了彻底转变,由以前的事后处理转变为事前预控和事中监测,整个生产过程的管控质量和决策质量取得了有效提升,极大地提高了生产时率和生产产量。
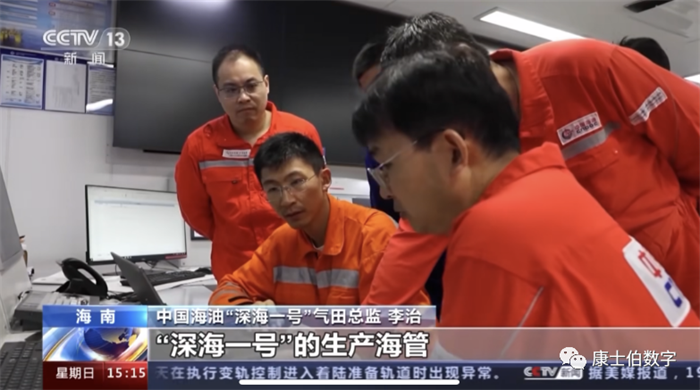
该系统还可用于解决不可测工艺参数的在线计算,工况动态预测,工况分析和设备状态监测。
将传统仪器仪表无法直接测量的生产数据,通过在线模拟计算的虚拟仪表,直观定量地展示给操作人员。例如管道的实时积液动态,药剂的浓度分布,水合物抑制剂效果,工艺流体的动态组分平衡等。将以往的监测盲区透明化,工艺分析颗粒度也更加的细化。
将设备状态监测与工艺动态相结合,与设备厂家针对撬装本身的分析工具实现了良好的互补结合。以往设备分析主要关注于分析设备本体的相关数据,与工艺数据的结合不深。通过系统中的设备状态分析算法,将外输压缩机和油嘴的工艺表现,与设备的工作状态结合,从工艺的角度反向评估设备运行的健康度。实现了伴随工艺生产的持续分析,对于工艺专业和设备维修专业的综合针对,给出了创新的解决方案。
将仪表偏差问题和潜在的风险信息,通过模型进行分析。这是以往仅通过人为的观察分析难以实现的。模型在持续计算和比对测量数据过程中,也在对每个仪表进行统计分析。同时,模型的计算结果也给了生产人员对于工艺变量的理论参考,帮助识别和分析出仪表数据后的生产价值。
工艺生产场景的定量分析,将以往在生产中通过经验探索或定性分析的场景,在动态模型上实现定量化、场景化的分析。例如,对丙烷丁烷在工艺系统中滞留问题的分析,通过模型实现实时动态的物料平衡分析。例如,解决压缩机流量计核验和产量匹配问题,通过压缩机模型实现虚拟流量计和流量匹配。例如,清管操作中的清管球位置跟踪,通过多相流清管模型,实现对清管球位置的在线显示。再例如,脱水脱烃工艺与上下游工艺操作设点之间的相关性分析,通过模型的离线模式,实现根据当前真实生产工况的流程模拟分析。随着气田的生产,类似的生产挑战和分析需求,均可考虑通过模型实现更加精确、定量的分析。
一体化生产管理系统的良好应用,体现了生产操作工具向着数字化、智能化方向的升级,体现了油气从业人员技术素养和专业能力的提升,是深水油气在数字化智能化转型中的成功落地。
更多详情,请关注“康士伯数字”微信公众号
郑重声明:文章仅代表原作者观点,不代表本站立场;如有侵权、违规,可直接反馈本站,我们将会作修改或删除处理。
相关阅读
猜你喜欢
-
新任国家发改委主任的能源电力往事!
2023-03-14 -
储能日报·速览【3月13日】
2023-03-14 -
风电每日报 | 3分钟·纵览风电事!(3月13日)
2023-03-14 -
4.8GW!2022年美国部署的储能系统创历史新高!
2023-03-14 -
102条!从两会议题看光伏、风电、储能等能源产业未来趋势!
2023-03-14 -
“两会”中的风电建言!
2023-03-14 -
全国政协委员、国家能源集团党组书记、董事长刘国跃:做好能源供应的“压舱石”
2023-03-14 -
东北能源监管局开展新型储能发展应用调研 研究落实市场机制支持政策
2023-03-14 -
海辰储能联合创始人、总经理王鹏程:未来三年是储能行业“生死卡位赛”
2023-03-13 -
辛保安赴国网北京电力检查工作并慰问干部员工
2023-03-13 -
日本计划一天排放500吨核废水入海!福岛核电站最新视频曝光!
2023-03-11 -
储能日报·速览【3月10日】
2023-03-11 -
广西最大水电站建成,粤、港、澳供水安全有保障!
2023-03-10 -
全国政协委员、国家能源集团董事长刘国跃:加快布局和释放煤炭优质产能
2023-03-10